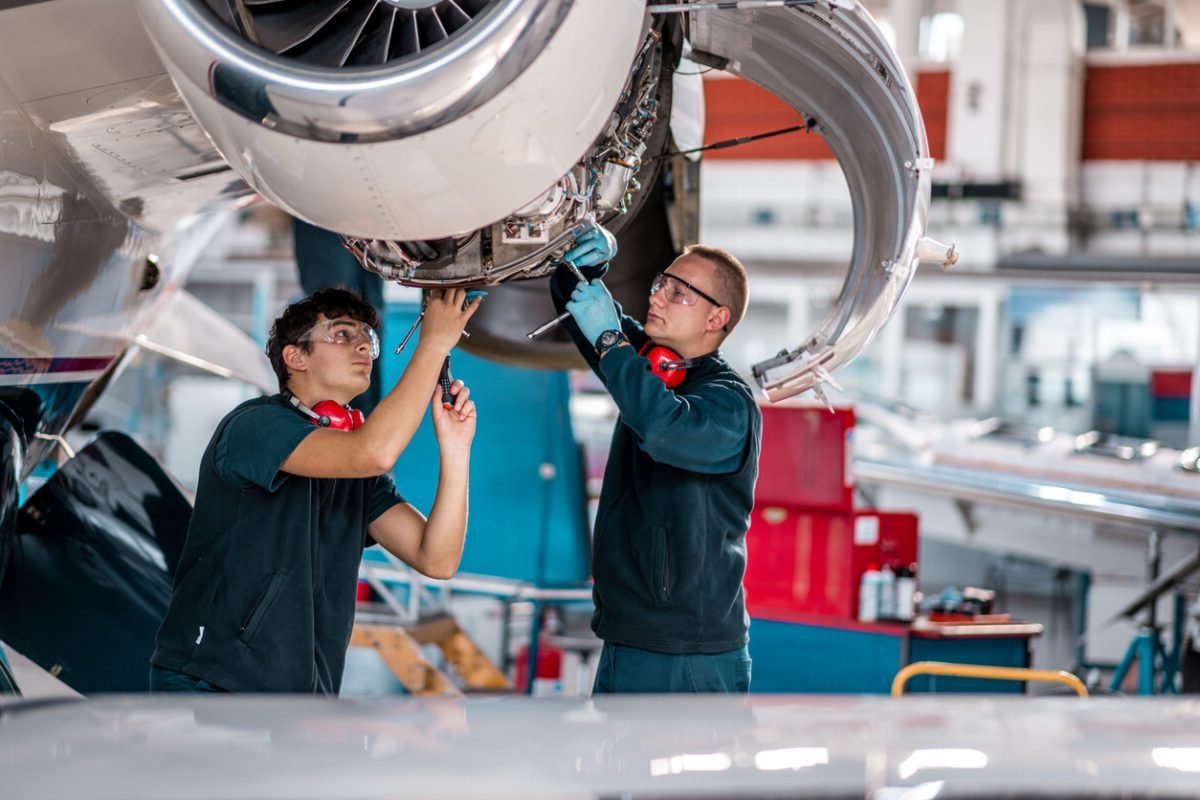
Operational efficiency is a term often thrown around in business circles, but what does it really mean? Simply put, it’s about getting the most out of your resources while minimizing waste. Imagine a well-oiled machine where every part works perfectly together, saving time and money. Operational efficiency isn't just for big corporations; small businesses can benefit too. From streamlining processes to adopting new technologies, there are countless ways to boost efficiency. Curious about how you can make your operations more efficient? Here are 14 facts that will help you understand and improve your business's operational efficiency.
Key Takeaways:
- Operational efficiency is about doing things in the best and cheapest way possible. It helps companies save money, make customers happy, and use resources wisely.
- To be efficient, companies need to measure how well they are doing, use smart strategies like Lean and Six Sigma, and help employees learn new skills.
What is Operational Efficiency?
Operational efficiency is the ability of an organization to deliver products or services to its customers in the most cost-effective manner while ensuring high quality. It involves optimizing processes, reducing waste, and maximizing resources.
-
Operational efficiency can significantly reduce costs by streamlining processes and eliminating unnecessary steps.
-
Companies that focus on operational efficiency often see improvements in customer satisfaction due to faster delivery times and higher quality products.
-
Automation plays a crucial role in enhancing operational efficiency by reducing human error and speeding up repetitive tasks.
Why is Operational Efficiency Important?
Understanding the importance of operational efficiency can help businesses stay competitive and profitable. It impacts various aspects of an organization, from financial performance to employee morale.
-
Efficient operations can lead to higher profit margins by reducing production costs and increasing output.
-
Employee productivity often increases when processes are optimized, as workers can focus on more value-added tasks.
-
Operational efficiency can also lead to better resource management, ensuring that materials and labor are used effectively.
How to Measure Operational Efficiency?
Measuring operational efficiency involves tracking key performance indicators (KPIs) that reflect the effectiveness of business processes. These metrics help identify areas for improvement.
-
Cycle time is a critical KPI that measures the time it takes to complete a process from start to finish.
-
Throughput measures the amount of product or service delivered over a specific period, indicating the efficiency of production processes.
-
Utilization rate tracks how effectively a company uses its resources, such as machinery and labor.
Strategies to Improve Operational Efficiency
Implementing strategies to improve operational efficiency can lead to significant benefits for an organization. These strategies often involve process optimization, technology adoption, and employee training.
-
Lean manufacturing techniques focus on reducing waste and improving process flow, leading to more efficient operations.
-
Six Sigma methodologies aim to reduce defects and variability in processes, enhancing overall efficiency.
-
Investing in employee training ensures that staff have the skills needed to perform their tasks efficiently and effectively.
Challenges in Achieving Operational Efficiency
While the benefits of operational efficiency are clear, achieving it can be challenging. Organizations must navigate various obstacles to optimize their processes successfully.
-
Resistance to change is a common challenge, as employees may be hesitant to adopt new processes or technologies.
-
Complexity of processes can make it difficult to identify inefficiencies and implement improvements.
Boosting Your Operational Efficiency
Operational efficiency isn't just a buzzword; it's a game-changer. Streamlining processes, cutting waste, and maximizing resources can transform your business. Start by analyzing workflows and identifying bottlenecks. Use technology to automate repetitive tasks and improve accuracy. Employee training is crucial—skilled workers are more productive and make fewer errors. Regularly review and adjust strategies to stay competitive. Remember, small changes can lead to significant improvements. Keep communication open and encourage feedback from your team. They often have valuable insights that can lead to better practices. Lastly, measure your progress. Use key performance indicators (KPIs) to track improvements and make data-driven decisions. By focusing on these areas, you'll see a noticeable boost in efficiency, leading to higher profits and a more robust business. Operational efficiency is within reach—take the steps to achieve it.
Frequently Asked Questions
Was this page helpful?
Our commitment to delivering trustworthy and engaging content is at the heart of what we do. Each fact on our site is contributed by real users like you, bringing a wealth of diverse insights and information. To ensure the highest standards of accuracy and reliability, our dedicated editors meticulously review each submission. This process guarantees that the facts we share are not only fascinating but also credible. Trust in our commitment to quality and authenticity as you explore and learn with us.