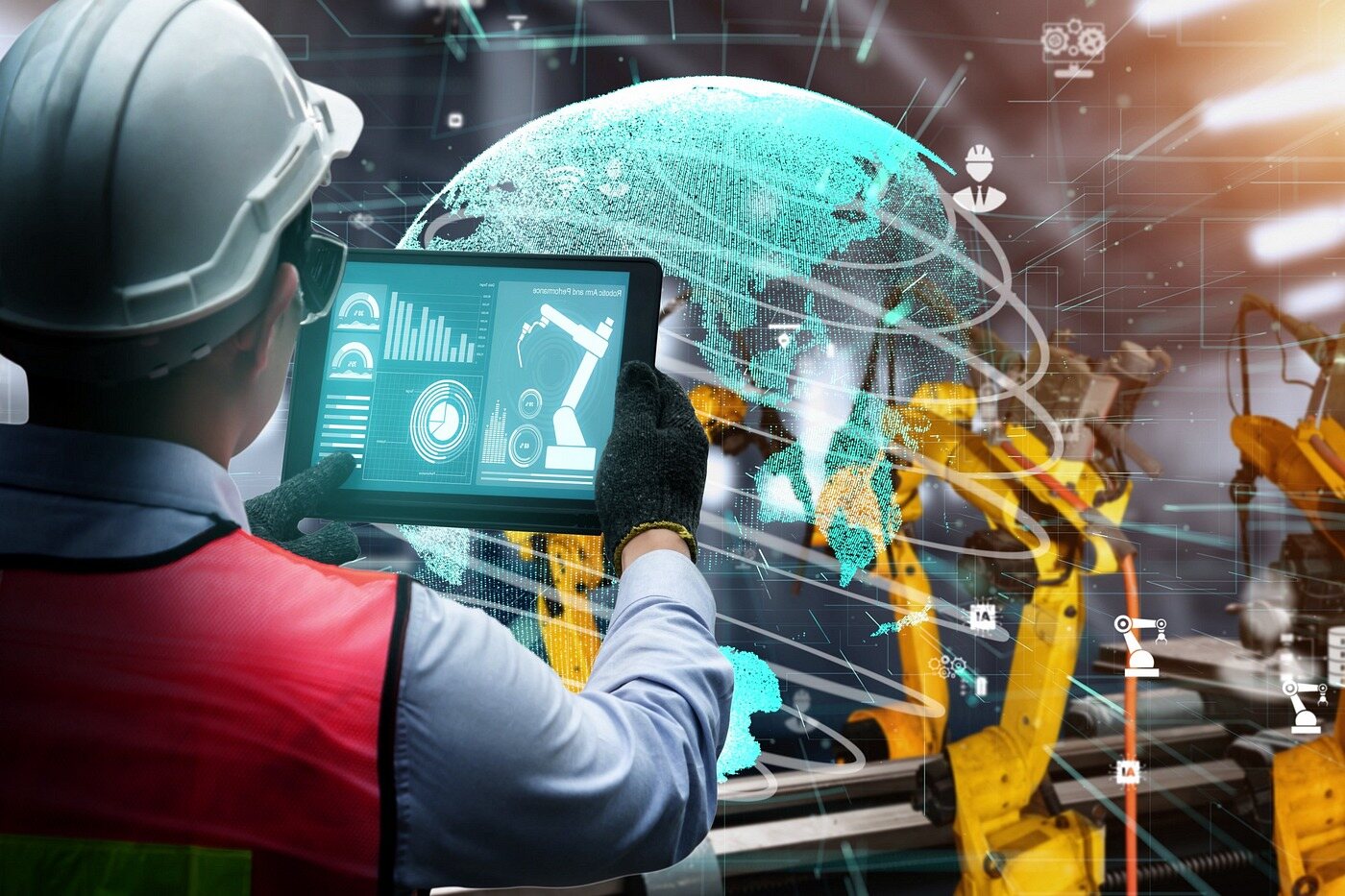
Predictive maintenance might sound like a futuristic concept, but it's already transforming industries today. What is predictive maintenance? It's a proactive approach that uses data analysis and machine learning to predict equipment failures before they happen. This method helps companies save money, reduce downtime, and extend the life of their machinery. Imagine knowing exactly when a machine will need repairs, allowing you to fix it before it breaks down. This approach is not just about fixing things; it's about optimizing performance and efficiency. By analyzing data from sensors and historical records, predictive maintenance can forecast potential issues, ensuring smooth operations. Industries like manufacturing, energy, and transportation are already reaping the benefits. As technology advances, more sectors will likely adopt this strategy, making it a game-changer in asset management. Curious about how it works and its impact? Let's dive deeper into this fascinating world of predictive maintenance.
What is Predictive Maintenance?
Predictive maintenance is a proactive approach that uses data analysis and monitoring to predict when equipment might fail. This method helps in planning maintenance activities before a breakdown occurs, saving time and resources.
-
Data-Driven Approach: Predictive maintenance relies heavily on data collected from various sensors and monitoring devices. This data is analyzed to predict potential failures.
-
Cost Savings: By preventing unexpected equipment failures, companies can save significant amounts of money on repairs and downtime.
-
Increased Equipment Lifespan: Regular maintenance based on predictive insights can extend the life of machinery by addressing issues before they escalate.
-
Improved Safety: Predictive maintenance can identify potential safety hazards, reducing the risk of accidents in the workplace.
-
Reduced Downtime: By scheduling maintenance activities at optimal times, businesses can minimize downtime and keep operations running smoothly.
How Does Predictive Maintenance Work?
Understanding the mechanics behind predictive maintenance can help businesses implement it effectively. It involves several steps and technologies that work together to predict equipment failures.
-
Condition Monitoring: This involves continuously monitoring the condition of equipment using sensors and other devices to detect anomalies.
-
Data Analysis: Advanced algorithms and machine learning models analyze the collected data to identify patterns and predict failures.
-
Machine Learning: Machine learning models improve over time, becoming more accurate in predicting equipment failures as they process more data.
-
Internet of Things (IoT): IoT devices play a crucial role in predictive maintenance by providing real-time data from equipment.
-
Cloud Computing: Cloud platforms store and process large amounts of data, making it accessible for analysis and decision-making.
Benefits of Predictive Maintenance
The advantages of predictive maintenance extend beyond just preventing equipment failures. It offers a range of benefits that can enhance overall business operations.
-
Optimized Maintenance Schedules: Maintenance activities are scheduled based on actual equipment needs rather than fixed intervals, leading to more efficient use of resources.
-
Better Resource Allocation: Companies can allocate resources more effectively, focusing on critical areas that require attention.
-
Enhanced Productivity: With fewer unexpected breakdowns, employees can focus on productive tasks, boosting overall productivity.
-
Environmental Impact: Predictive maintenance can reduce waste and energy consumption by ensuring equipment operates efficiently.
-
Customer Satisfaction: Reliable operations lead to better service delivery, enhancing customer satisfaction and loyalty.
Challenges in Implementing Predictive Maintenance
While predictive maintenance offers numerous benefits, implementing it can be challenging. Understanding these challenges can help businesses prepare and overcome them.
-
High Initial Costs: Setting up predictive maintenance systems can be expensive due to the need for advanced technology and skilled personnel.
-
Data Management: Handling large volumes of data requires robust data management systems and expertise.
-
Integration with Existing Systems: Integrating predictive maintenance with existing systems can be complex and time-consuming.
-
Skill Requirements: Implementing and managing predictive maintenance requires specialized skills and training.
-
Data Security: Protecting sensitive data from cyber threats is a major concern for businesses adopting predictive maintenance.
Future of Predictive Maintenance
As technology advances, predictive maintenance is expected to evolve, offering even more sophisticated solutions for businesses.
-
AI Advancements: Artificial intelligence will play a larger role in predictive maintenance, providing more accurate predictions and insights.
-
Increased Automation: Automation will reduce the need for manual intervention, making predictive maintenance more efficient.
-
Wider Adoption: As costs decrease and technology becomes more accessible, more industries will adopt predictive maintenance.
-
Integration with Digital Twins: Digital twins, virtual replicas of physical assets, will enhance predictive maintenance by providing detailed insights into equipment performance.
-
Sustainability Focus: Predictive maintenance will contribute to sustainability efforts by reducing waste and energy consumption.
-
Real-Time Monitoring: Advances in technology will enable real-time monitoring and instant alerts for potential issues.
-
Customized Solutions: Predictive maintenance solutions will become more tailored to specific industry needs, providing more relevant insights and recommendations.
The Future of Predictive Maintenance
Predictive maintenance is changing how industries handle equipment care. By using data analysis and machine learning, businesses can spot potential problems before they become costly failures. This approach not only saves money but also boosts efficiency and safety. As technology advances, predictive maintenance will become even more precise, offering real-time insights and reducing downtime. Companies adopting these strategies will likely see a competitive edge, as they can maintain operations smoothly and respond quickly to issues. While challenges like data management and integration exist, the benefits far outweigh the hurdles. Embracing predictive maintenance is a smart move for any industry looking to improve reliability and performance. As more sectors recognize its value, this method will become a standard practice, ensuring equipment runs optimally and businesses thrive.
Was this page helpful?
Our commitment to delivering trustworthy and engaging content is at the heart of what we do. Each fact on our site is contributed by real users like you, bringing a wealth of diverse insights and information. To ensure the highest standards of accuracy and reliability, our dedicated editors meticulously review each submission. This process guarantees that the facts we share are not only fascinating but also credible. Trust in our commitment to quality and authenticity as you explore and learn with us.