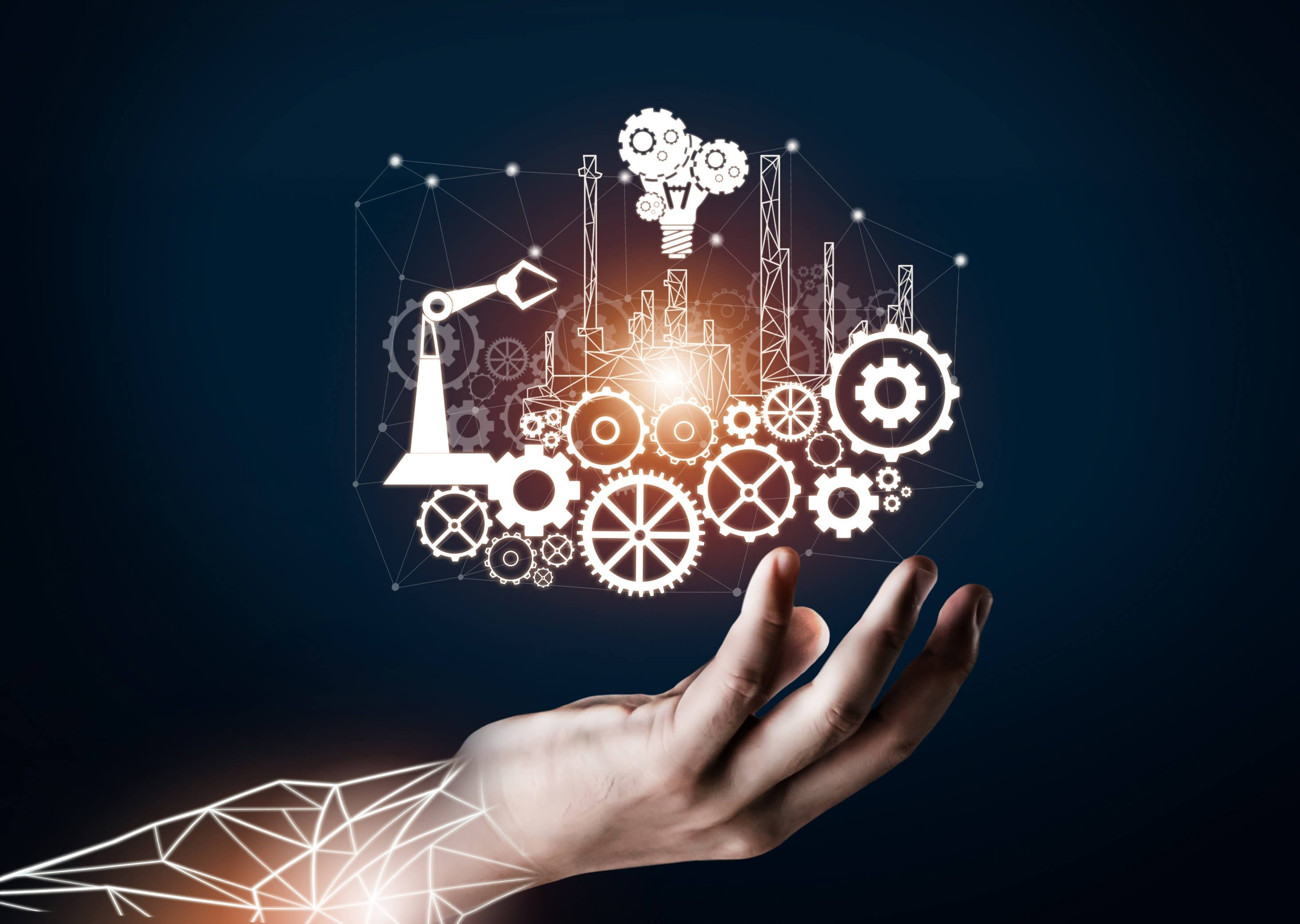
What is operational efficiency? It's all about doing things smarter, not harder. Imagine a factory where every machine hums perfectly, every worker knows their role, and waste is minimized. That's operational efficiency in action. It's the secret sauce that helps businesses save money, time, and resources while boosting productivity. Companies aim to streamline processes, cut unnecessary steps, and make the most of what they have. This means less waste, faster production, and happier customers. In today's fast-paced world, being efficient isn't just a nice-to-have—it's a must. Whether it's a small business or a giant corporation, operational efficiency can make a big difference. Curious about how it works and why it matters? Let's dive into the world of operational efficiency and see how it can transform the way things get done.
Understanding Operational Efficiency
Operational efficiency is all about getting the most out of resources while minimizing waste. It's a key concept in business, helping companies save money and time. Let's explore some fascinating facts about this important topic.
-
Efficiency vs. Effectiveness: Efficiency is about doing things right, while effectiveness is about doing the right things. Both are crucial, but efficiency focuses on the process and resources.
-
Lean Manufacturing: This approach aims to maximize productivity by reducing waste. Originating from Toyota, it has transformed industries worldwide.
-
Six Sigma: A set of techniques and tools for process improvement, Six Sigma seeks to improve quality by identifying and removing causes of defects.
-
Kaizen Philosophy: This Japanese term means "continuous improvement." It encourages small, incremental changes that lead to significant improvements over time.
-
Automation's Role: Automation can significantly boost efficiency by handling repetitive tasks, allowing human workers to focus on more complex activities.
-
Energy Efficiency: Reducing energy consumption not only cuts costs but also benefits the environment. Many companies are investing in energy-efficient technologies.
Measuring Operational Efficiency
Measuring efficiency involves assessing how well resources are used to achieve goals. Various metrics and tools help businesses track their performance.
-
Key Performance Indicators (KPIs): KPIs are metrics used to evaluate success. Common KPIs for efficiency include cycle time, throughput, and resource utilization.
-
Benchmarking: Comparing a company's performance against industry standards or competitors helps identify areas for improvement.
-
Total Quality Management (TQM): TQM focuses on long-term success through customer satisfaction. It involves all members of an organization in improving processes, products, and services.
-
Balanced Scorecard: This strategic planning tool provides a comprehensive view of an organization's performance by measuring financial and non-financial metrics.
-
Cost-Benefit Analysis: This method evaluates the financial implications of decisions, helping businesses choose the most efficient options.
Improving Operational Efficiency
Improving efficiency requires a strategic approach and a willingness to adapt. Here are some methods companies use to enhance their operations.
-
Process Mapping: Visualizing processes helps identify bottlenecks and areas for improvement, leading to more streamlined operations.
-
Employee Training: Well-trained employees are more efficient. Investing in training programs can lead to significant productivity gains.
-
Technology Integration: Implementing the latest technology can automate tasks, improve communication, and enhance overall efficiency.
-
Supply Chain Optimization: Streamlining the supply chain reduces costs and improves delivery times, boosting overall efficiency.
-
Outsourcing: By outsourcing non-core activities, companies can focus on their strengths and improve efficiency.
Challenges in Achieving Operational Efficiency
Despite its benefits, achieving operational efficiency can be challenging. Companies must navigate various obstacles to succeed.
-
Resistance to Change: Employees may resist new processes or technologies, hindering efficiency efforts.
-
Resource Constraints: Limited resources can make it difficult to implement efficiency improvements.
-
Complexity: As organizations grow, processes can become more complex, making it harder to maintain efficiency.
-
Data Overload: With the rise of big data, companies may struggle to analyze and use information effectively.
-
Regulatory Compliance: Adhering to regulations can be time-consuming and costly, impacting efficiency.
Real-World Examples of Operational Efficiency
Many companies have successfully improved their efficiency, setting examples for others to follow.
-
Toyota: Known for its lean manufacturing approach, Toyota has become a leader in operational efficiency.
-
Amazon: By optimizing its supply chain and using advanced technology, Amazon has revolutionized the retail industry.
-
Apple: Apple's focus on design and innovation has led to streamlined processes and efficient production.
-
Walmart: Through supply chain optimization and technology integration, Walmart has maintained its position as a retail giant.
-
General Electric: GE's commitment to Six Sigma has resulted in significant improvements in quality and efficiency.
The Final Word on Operational Efficiency
Operational efficiency is all about making things run smoother and faster. It's not just for big companies; even small businesses can benefit. By focusing on process improvement, you can cut costs and boost productivity. This means looking at how tasks are done and finding ways to do them better. Technology plays a big role too. Using the right tools can automate repetitive tasks, freeing up time for more important work. Employee training is another key factor. When workers know what they're doing, they're more efficient. Don't forget about customer feedback. Listening to what customers say can help you improve services and products. Lastly, keep an eye on metrics. Tracking performance helps you see what's working and what needs fixing. In the end, operational efficiency is about doing more with less and keeping everyone happy.
Was this page helpful?
Our commitment to delivering trustworthy and engaging content is at the heart of what we do. Each fact on our site is contributed by real users like you, bringing a wealth of diverse insights and information. To ensure the highest standards of accuracy and reliability, our dedicated editors meticulously review each submission. This process guarantees that the facts we share are not only fascinating but also credible. Trust in our commitment to quality and authenticity as you explore and learn with us.